The composition of silicate series cement can be categorized into raw materials for producing silicate cement clinker, gypsum, and mixed materials.
(1) Composition materials of silicate series cement clinker
Silicate series cement clinker comprises lime raw materials, clay raw materials, and iron ore powder.
The lime raw materials are natural limestone, tuff and shells, which mainly provide CaO in cement; the clay raw materials are primarily clay (or shale, mudstone, siltstone, and river mud), whose main component is SiO₂, followed by Al₂O₃ and a small amount of FezO₃; the iron ore powder is hematite, whose chemical composition is Fe₂O₃, which mainly makes up for the lack of iron content in clay. In cement raw materials, the content of various components must meet the following requirements.
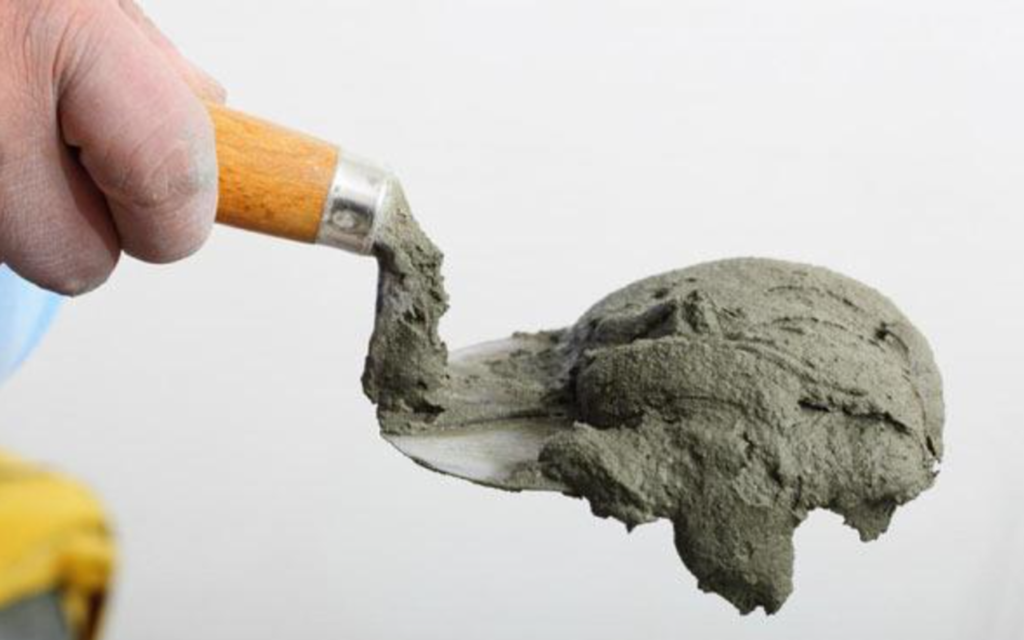
CaO 62%~67%
SiO₂ 20%~24%
Al₂O₃ 4%~7%
Fe₂O₃ 2.5%~6.0%
(2) Gypsum
When producing cement, must add an appropriate amount of gypsum to delay the setting of cement. In silicate cement and ordinary silicate cement, gypsum mainly plays a retarding role. In cement with a large amount of mixed materials, gypsum also plays a role in stimulating the activity of mixed materials. The gypsum added to cement is mainly natural gypsum anhydrous calcium sulfate.
(3) Mixed materials
To improve cement’s performance, adjust the cement’s strength grade, increase cement output, and expand the variety of cement, various mineral materials that must be added during cement production are called mixed materials. Mixed materials can be divided into two categories: active mixed materials and inactive mixed materials.
Active mixed materials refer to mineral materials with potential hydraulic or volcanic ash properties or both volcanic ash properties and hydraulic properties. Volcanic ash properties refer to the property that a material, after being ground into fine powder, does not have hydraulic properties alone but can form a hydraulic compound after being mixed with lime and water at room temperature. Common types of active mixed materials include granulated blast furnace slag, volcanic ash mixed materials, and fly ash. Granulated blast furnace slag is a melt with silicate and calcium aluminate as the main components. After water quenching and granulation, its chemical composition is mainly CaO, Al2O2, and SiO2, accounting for more than 90% of the total mass. It also contains a small amount of MgO, Fe2O2, and some sulfides. When quenched and granulated, the slag forms an unstable glass body and has potential hydraulic properties. Slow-cooled slag is not hydraulic.
Volcanic ash mixed materials refer to natural or artificial mineral materials with volcanic ash characteristics. It can be divided into three categories:
·hydrous silicate materials (diatomaceous earth, diatomite)
·burnt clay materials (burnt clay, coal slag, fly ash)
·volcanic ash materials (volcanic ash, tuff)
Fly ash is an industrial waste from thermal power plants. It is a fine-grained waste residue discharged from coal-fired boilers. It is mainly composed of SiO₂ and Al₂O₃, contains a small amount of CaO, and has the characteristics of volcanic ash.
Inactive mixed materials refer to mixed materials that do not have potential hydraulic hardness or whose quality activity index cannot meet the specified requirements. Common varieties include slow-cooled slag, ground quartz sand, and limestone powder. This type of mixed material is added to cement mainly to play a filling role, which can increase cement output, reduce the hydration heat and strength grade, and have little effect on other properties of cement.
(4) Mineral composition and performance requirements of silicate cement clinker
Silicate series cement clinker is a hydraulic cementitious material with calcium silicate as the main mineral component. It is obtained by grinding raw materials mainly containing CaO, SiO₂, Al₂O₃, and Fe₂O₃ into fine powder according to appropriate proportions and burning until partially melted.
According to its main characteristics and uses, silicate cement clinker can be divided into general purpose, medium sulfate resistance, medium hydration heat, and high sulfate resistance.
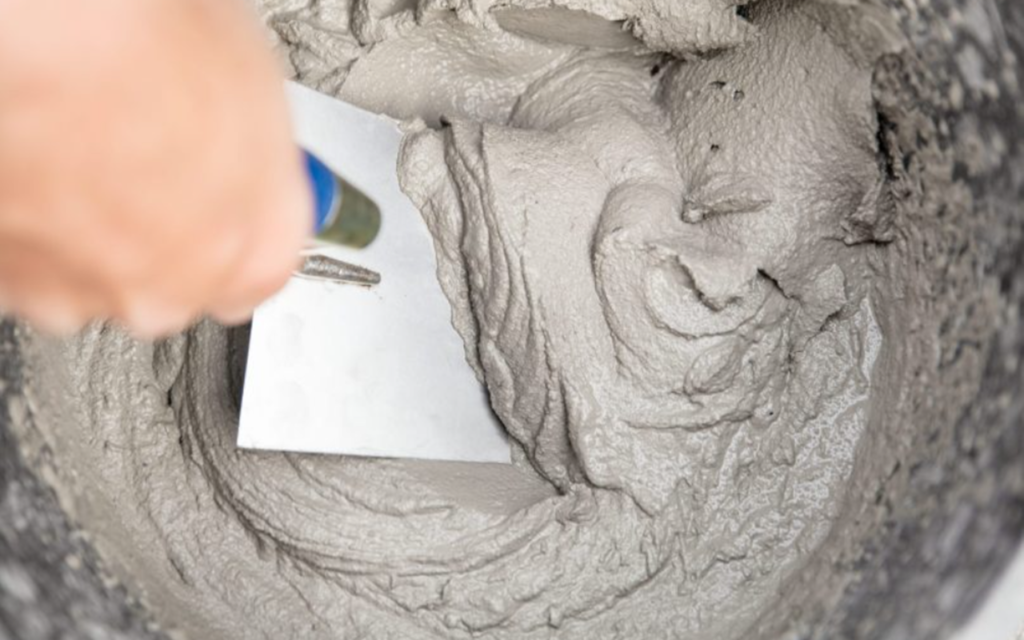
The quality standards for silicate cement clinker are stringent, ensuring its reliability and performance. The setting time should not be earlier than 45min, and the final setting should not be later than 6.5h. The stability is tested and qualified using the boiling method. The compressive strength should meet or exceed the requirements of Table 2-11. Importantly, all types of silicate cement clinker are strictly prohibited from containing any foreign matter, guaranteeing its purity and consistency.
Coagulation and hardening of silicate cement
After adding an appropriate amount of water to cement paste, due to its own physical and chemical changes, it will gradually become thicker and lose plasticity, but it does not yet have strength. This process is called cement “coagulation.” As time goes by, its strength continues to develop and increase, gradually turning into a hard stone-like substance—cement stone. This process is called cement “hardening.” Cement coagulation and hardening are continuous and complex physical and chemical change processes that cannot be separated.
(1) Hydration of silicate cement
Upon the addition of water to cement, a dynamic reaction ensues. The clinker minerals within the cement swiftly react with water, a process known as hydration and hydrolysis. This reaction is not only transformative but also dynamic, generating a series of new compounds and releasing a significant amount of heat. The reaction unfolds as follows:
2(3CaO·SiO₂)+6H₂O=—3CaO·2SiO₂·3H₂O+3Ca(OH)₂
2(2CaO·SiO₂)+4H₂O=3CaO·2SiO₂ ·3H₂O+Ca(OH)₂
3CaO·Al₂O₃+6H₂O==3CaO·Al₂O₃·6H₂O
4CaO·Al₂O₃·Fe₂O₃+7H₂O
3CaO·Al₂O₃·6H₂O+CaO·Fe₂O₃·H₂O
3CaO·Al₂O₃·6H₂O+3(CaSO₄·2H₂O)+19H₂O
3CaO·Al₂O₃·3CaSO₄·31H₂O
In summary, after silicate cement reacts with water, the main hydrates are hydrated silicate, hydrated calcium ferrite gel, calcium hydroxide, hydrated calcium aluminate, and hydrated calcium sulfoaluminate crystals. These hydration products determine a series of properties of cement paste.
(2) The setting and hardening process of silicate cement
When cement is mixed with water, a hydration reaction immediately occurs on the surface of cement particles. This reaction is crucial as it initiates the process. The hydration products dissolve in water, a key medium for the reaction. Then the cement particles expose a new layer of surface and continue to react with water, so that the solution around the cement particles quickly becomes a saturated solution of hydration products. This saturation is a significant point in the process. After the solution has reached saturation, the products generated by the continued hydration of cement can no longer dissolve, and many fine dispersed particles precipitate to form a gel. This gel formation is a critical step. As the hydration reaction continues, the new colloid particles continue to increase, and the free water continues to decrease, making the gel gradually thicker and the cement paste gradually lose its plasticity, that is, coagulation occurs. This coagulation is a major change in the process. After that, the calcium hydroxide and hydrated calcium aluminate in the gel will gradually turn into crystals, run through the gel, and combine tightly to form a cement paste with a certain strength. This crystal formation is a significant development. As the hardening time continues, the unhydrated part inside the cement particles will continue to hydrate, so that the crystals gradually increase, the gel gradually becomes dense, and the cement paste has higher and higher bonding power and strength. This increase in strength is a key outcome. In addition, when cement solidifies and hardens in the air, the calcium hydroxide formed by the hydration of its surface reacts with the carbon dioxide in the air to form a thin layer of calcium carbonate (CaCO₃), which is called carbonation.
From the above process, it can be seen that the hydration reaction of cement gradually penetrates from the surface of the particles to the inner layer. It starts faster. Later, due to the formation of a gel film on the surface of the cement particles, it becomes more and more difficult for water to penetrate, and the hydration becomes slower and slower. The practice has proved that it takes several years or even decades to complete the whole process of cement hydration and hydrolysis. This is a significant time frame. Generally, cement hydrates and hydrolyzes quickly within the first 3 to 7 days, so its strength increases faster. This is the initial rapid stage. The basic part of this process can be completed within 28 days. This is the first month. After that, it slows down significantly and the strength increase is also extremely slow. This is the long-term slow stage.