Methyl cellulose is a general term for a type of cellulose ether whose primary substituent is methyl, including single ether methylcellulose (MC), hydroxyethyl methyl cellulose (HEMC), hydroxypropyl methylcellulose Cellulose mixed ethers such as hydroxy butyl methylcellulose (HPMC), hydroxy butyl methyl cellulose (HBMC), ethyl methyl cellulose (EMC) and carboxymethyl methyl cellulose (CMMC) all have properties similar to MC, that is, thermal gelation will occur in water below 100°C.
The gel temperature of water-soluble MC decreases with increasing DS. A typical MC (DS=1.8) forms a gel at 54-56°C. Due to uneven substitution, MC solutions usually contain insoluble colloidal particles or fiber filaments. To obtain a product with a higher DS value, high gelling temperature, and an obvious solution, special alkalization can be carried out by using NaOH-Cu(Ⅱ) complex or trimethyl benzyl ammonium hydroxide as an alkalizing reagent. These reactants make alkali cellulose fully swollen, greatly enhancing the accessibility of cellulose macromolecules during etherification. However, this technology has not been industrialized due to technical and cost reasons.
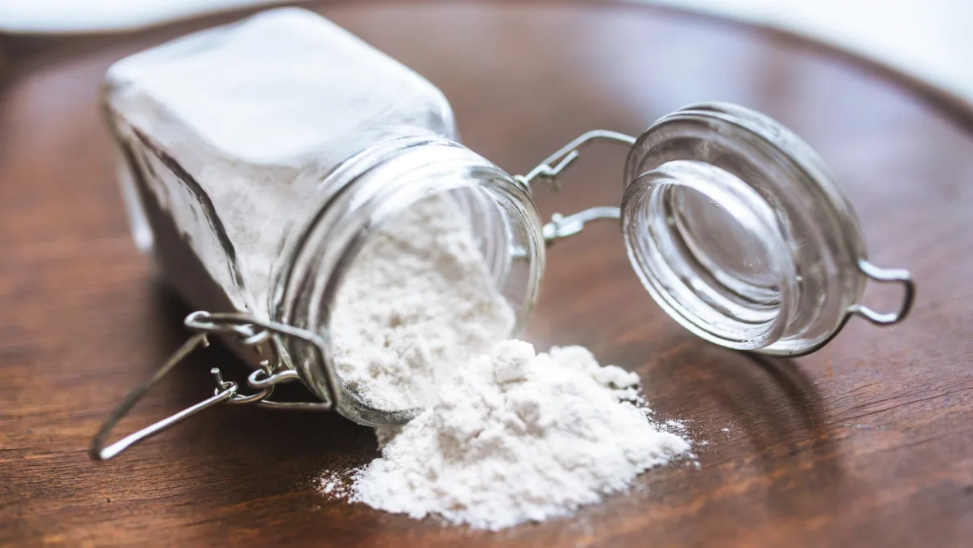
Substitution by using mixed groups is the most effective method to improve product solubility and gel temperature. Many products with different properties can be obtained by adjusting the ratio of methyl and second substituents. Among these mixed ethers, the most important and common ones are hydroxypropyl methylcellulose (HPMC) and hydroxyethyl methylcellulose (HEMC). They are mixed ethers prepared by introducing hydroxyalkyl groups on alkali cellulose with propylene or ethylene oxide. Taking HPMC as an example, there are many types, and the group substitution has a wide range: the DS value of the methyl group is 1.3~2.2, and the MS value of the hydroxypropyl group is 0.1~0.8. HEMC is mainly produced in Europe. The DS value of the methyl group is 1.5~2.0, and the MS value of the hydroxyethyl group is 0.02~0.3. Hydroxybutyl methylcellulose (HBMC) is obtained by hydroxymethylation with butylene oxide. The DS of hydroxybutyl is 0.04~0.1. For general methylation (DS=1.8~2.2), HBMC is an oil-soluble ether. Another product in the UK is water-soluble ethyl methylcellulose (EMC), with a DS of 0.9 for the methyl group and 0.4 for the ethyl group. In addition, carboxy methylmethyl cellulose (CMMC) has weak anionic polyelectrolyte properties.
Even if the substitution level is shallow after secondary substitution, the resulting methyl cellulose mixed ether solution is more straightforward and transparent than the MC solution; the gelation temperature increases, especially when hydrophilic carboxymethyl or hydroxyethyl groups are introduced. It is generally not desirable to have a gelation temperature higher than 95°C because a too high temperature will make it difficult to remove the residual salt in the system by washing it with hot water.
The production of methylcellulose and its mixed ethers requires large amounts of alkali. To obtain water-soluble ether, the material ratio of NaOH to anhydroglucose units should be 3 to 4, and the DS of the methyl group should be 1. 4 to 2. 0. The viscosity of the material is adjusted by controlling the oxygen concentration during alkalization (aging). An excess of methyl chloride (depending on the base amount) will convert all the NaOH to NaCl. The product is almost neutral and requires little or no acid neutralization. Methanol and dimethyl ether by-products are produced by reacting methyl chloride with water. The main processes are as follows:
(1)Gaseous methylation process
Alkali cellulose and partial methyl chloride are heated to 50°C in a corrosion-resistant pressure vessel equipped with efficient mixing to initiate methylation. Through moderate heat supplementation (heating or cooling), the exothermic etherification reaction temperature can be maintained at 60 to 100°C for several hours.
During the production process, some reactants evaporate along with volatile by-products. These substances should be separated, condensed, and recovered as needed. The recovered methyl chloride is then recycled with new reactants to ensure that the concentration of gaseous chloride in the reaction vessel is constant. The blades and shafts of the stirrers used by some manufacturers are hollow and porous, and the reactants directly enter the reaction system after being recovered.
(2)Liquid methylation process
The continuous process using liquid methyl chloride requires a reaction time of less than 1 hour. This process is carried out in a large number of reaction reagents. Alkaline cellulose is slurried under pressure, and a heated tubular reactor is used to pump the slurry away to evaporate volatile by-products and excess reactants.
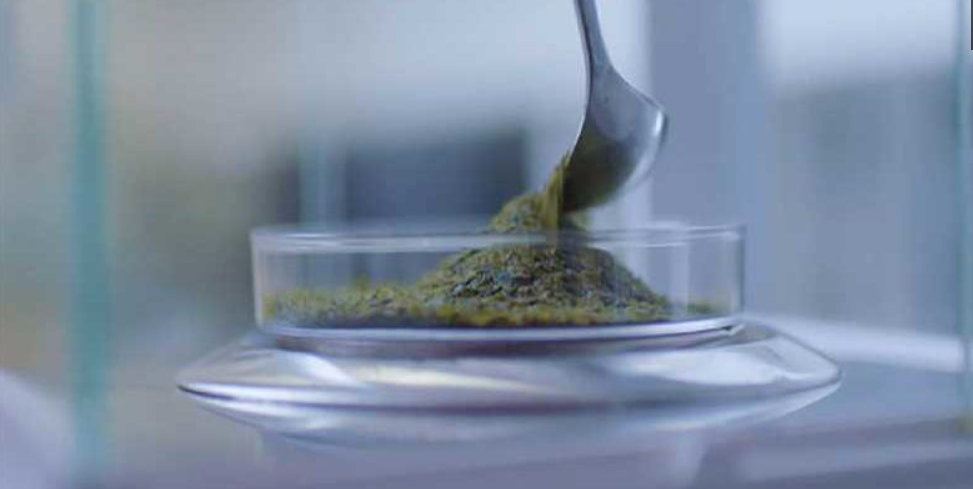
Other liquid phase processes and technologies are carried out in the presence of a large amount of inert organic liquid. This method can reduce the reaction pressure and promote heat exchange. A small amount of alkali is required during the reaction, which inhibits the formation of by-products.
All these processes are suitable for the production of mixed ethers. The second reactant can be added before or after the start of methylation. The best method is to gradually add the etherifying agent and control the temperature of the reaction system in steps.
NaCl and non-volatile by-products (such as propylene glycol) are removed by washing with hot water, and then the product is dried in ordinary drying equipment. Typically, MC products contain less than 1% NaCl, and high-purity products contain less than 0.1% NaCl. Products with very low viscosity can be obtained by acid treatment, and products with controllable solubility can be adjusted through cross-linking reac