Dry-mixed mortar can be divided into packaged dry-mixed mortar and bulk dry-mixed mortar. The former is packed in 25kg plastic woven bags or composite kraft paper bags, while the latter is transported in bulk trucks and to steel storage tanks under pressure.
Mixing of dry-mixed mortar
Dry-mixed mortar should be mixed mechanically, and portable mixers can also be used for bagged dry-mixed mortar. The amount of water added during mixing should be within the range of the water added in the formula design.
A spiral mixer integrated with the storage tank can stir bulk dry-mixed mortar. The equipment should be able to work continuously, and the mixing volume should be at least 50kg/min.
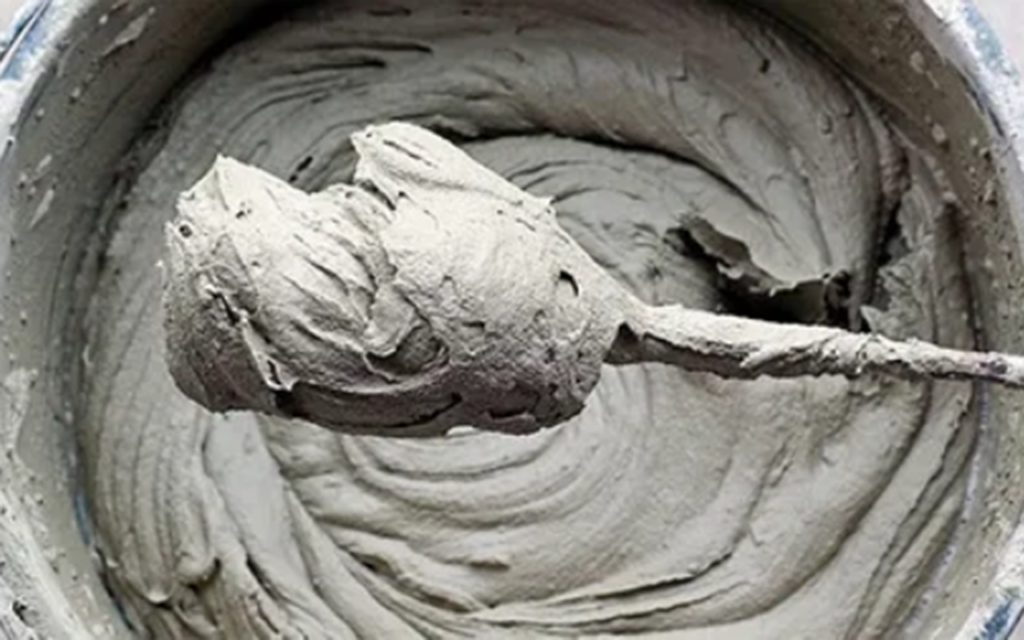
If a continuous mixer is used for dry-mixed mortar, the amount of water added required by the product manual should be used as the basis, and the amount of mixing water should be fine-tuned according to the consistency of the on-site construction; if a portable electric mixer is used for dry-mixed mortar, the amount of water added required by the product manual should be strictly followed. To stir, first put the specified amount of mixing water in the container, then add the dry-mixed mortar one after another while stirring continuously. The mixing time should be 3min to 5min. Stop for 10 minutes and then stir for another 0.5 minutes. The consistency should meet relevant provisions of current construction regulations. Dry-mixed mortar should be mixed and used. No other ingredients need to be added except water. Users are not allowed to add certain ingredients to change the purpose and grade of dry-mixed mortar.
Construction of dry-mixed mortar for masonry
The mortar used in building masonry and other various blocks is called masonry mortar. Masonry mortar is an essential part of masonry. Whether it is load-bearing or non-load-bearing masonry, mortar plays a vital role in the masonry structure and has a significant influence. Dry-mixed mortar for masonry can not only overcome the shortcomings of traditional construction methods that are difficult to control cracking due to dry and wet cycles of wall materials but can also meet the requirements for firmness, stability, and durability of wall masonry, thus not only facilitating construction but also ensuring and improving engineering construction quality.
General provisions for masonry dry-mixed mortar construction
The mixed mortar mixture should be used up within the time specified in the instruction manual. In hot or windy weather, measures should be taken to prevent water evaporating too quickly. After the initial setting time is exceeded, it is strictly prohibited to add water to mix again. When the ambient temperature and the temperature of the construction base surface are lower than 5℃, construction cannot be carried out without effective insulation and antifreeze measures. If rain or snow suddenly occurs during construction, effective measures should be taken to prevent rain and snow from damaging the uncondensed mortar. Falling ash must be recycled and used promptly. If it exceeds the initial setting time, reuse is strictly prohibited.
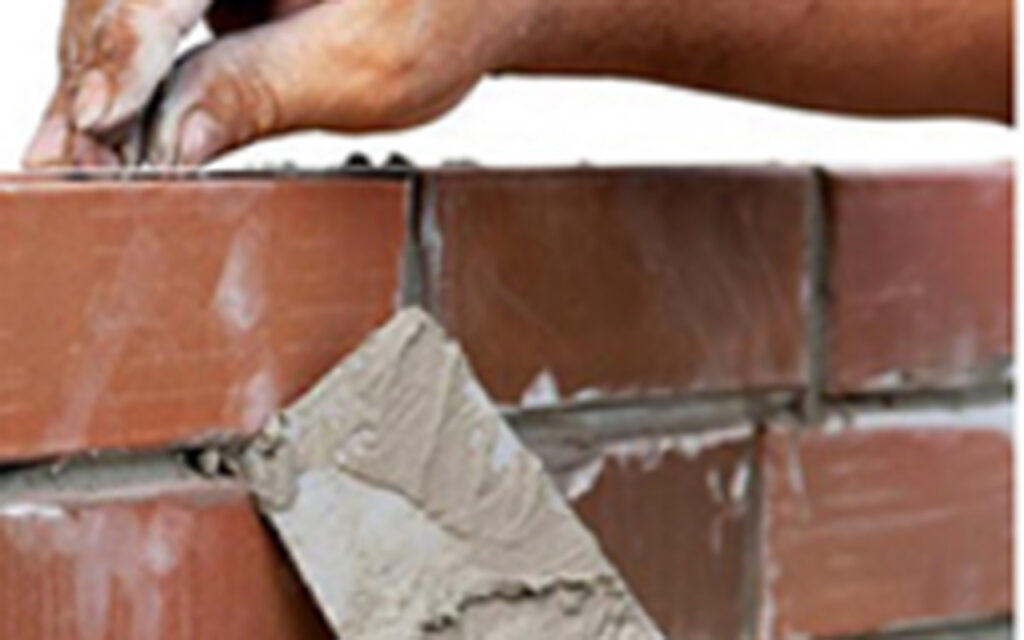
a. The materials used in masonry projects should have quality certificates and meet the design requirements. If there are retest requirements, they should be used only after passing the retest. Bricks and blocks used in masonry projects should comply with corresponding standards.
b. Dry-mixed mortar can join the wall with the original slurry but must be hooked along with the construction. The dry-mixed powder mortar used should comply with relevant standards and local regulations.
c. The consistency of the masonry mortar should be determined according to the type of block material, climatic conditions, and construction technology, as well as through trial masonry.
d. The mortar should be mixed and used immediately. After mixing, the mortar should be used within 3 to 4 hours. When the maximum temperature during construction exceeds 30°C, it should be used within 2 hours.
e. During masonry construction, the vertical structure should be marked according to the design requirements, block material specifications, and mortar joint thickness. The flatness, verticality, mortar joint thickness, and mortar fullness of the masonry surface should be controlled. Masonry surface flatness and verticality must be corrected before the mortar has set.