Since recently, all iron oxide pigments manufactured at its Krefeld-Uerdingen site in Germany, Lanxess has been offering environmental product declarations verified by the German Institute for Construction and the Environment (IBU) since the beginning of the year. These make it easier for construction product manufacturers to more accurately determine the environmental impact of their products. And in the near future, the specialty chemicals company is also set to significantly reduce the carbon footprint of its granulated iron oxide yellow pigments by using “green” sodium hydroxide. All these measures are designed to make it easier for customers and, for example, manufacturers of concrete building materials and products, to implement a more sustainable product strategy along the value chain.
Sustainable construction is a vital part of the journey toward a climate- and resource-friendly future, which is why increasing focus is being placed on the environmental footprint of buildings – whether in public-sector construction projects or industrial and private residential projects. The entire building life-cycle – from the construction and usage phases through to demolition and disposal – is put under the microscope. Environmental product declarations (EPDs) have become increasingly widespread over the past few years as a way of quantifying and communicating the environmental footprint of construction products. They constitute the foundation of consistent life-cycle assessments for entire buildings. This trend is set to increase in the future because many certification systems for sustainable construction reward the use of construction products with EPDs – for example, from the German Sustainable Building Council (DGNB). Around 1,500 EPDs from around 500 declaration holders, for example, have already been issued by the IBU alone – and this figure is set to increase over time. Harmonization at the European level is ensured through collaboration among local EPD program operators as part of the ECOPlatform initiative.
EPDs describe how construction materials, products and components impact the environment throughout their entire life-cycle. They are based on life-cycle assessments and, as such, reflect the sum of all environmental impact factors of the construction materials used. They assess, for example, the extent to which the manufacture and use of building materials and the processes at the end of their life-cycles contribute to the greenhouse effect and acid rain; how much water is used in the manufacturing process; and the proportion of recycled material. The success of EPDs in recent years has been due in no small part to the fact that, thanks to the Product Category Rules (PCR), standardized and specific rules regarding their calculation and creation have already long been in place and also subject to ongoing harmonization – including at the cross-product level – thanks in particular to European standard EN 15804. This creates a credible and reliable foundation with harmonized assessment parameters so that, with the help of standardized data, the sustainability of construction projects can be evaluated and compared.
EPDs have proved their worth
EPDs offer myriad benefits for building material manufacturers, allowing them to document and demonstrate their sustainability efforts. Using the manufacturers’ data, their customers can, in turn, prepare building life-cycle assessments and compare construction methods and products in an eco-friendly way. They also open a range of market opportunities because construction tenders increasingly require EPDs, especially when the aim is to obtain building certificates. In the future, EPDs could act as a kind of “entry ticket” into the European construction market. After all, the draft of the New European Construction Products Regulation contains provisions allowing most indicators required in EPDs to also be incorporated in the declaration of performance for construction products. Last but not least, EPDs give building material manufacturers the opportunity to analyze and optimize the environmental footprint of their value chains in terms of processes and materials.
Trend toward EPDs for raw materials and construction products
So far, EPDs have been prepared mainly for finished construction products as a way of gaining comparable and reliable data concerning the environmental impact of buildings. EPD verification has traditionally paid almost no attention, however, to the raw materials for construction products – with the exception of precursors that, due to complex chemical processes or extremely energy-intensive production steps, play a dominant role in the life-cycle assessment of a construction product. One example here is cement, which accounts for more than 80 percent of the green-house gas emissions from concrete.
Since no up-to-date EPD data has ever been available for many of the raw materials used in construction products, it has frequently been necessary to use generic values that often reflect only some vague average and are also erroneous. A few years ago, for example, the association for the mineral pigments industry stated that the average carbon footprint of inorganic pigments used for coloring cement-based building materials was around six kilograms of CO2 equivalents per kilogram of product / ±50 percent. The EPD-verified values for Lanxess iron oxide pigments are much lower, however, which can be attributed also to the specialty chemicals company’s continuous investment in energy-efficient processes (Figure 2). So, there is increasing awareness on the market that precise EPD data for raw materials significantly improve the accuracy, quality. and credibility of construction product EPD data and building life-cycle assessments. This has since been recognized by lawmakers, too. The draft of the New European Construction Products Regulation contains regulations obligating suppliers of construction product manufacturers to provide verified data concerning the environmental footprint of raw materials.
Successful market launch
Lanxess expressly welcomes the trend toward EPD-certified raw materials. In early 2022, the company became the first manufacturer of iron oxide pigments anywhere in the world to launch products with EPD verification from the IBU and is set to expand this offering across its entire range of red, yellow, and black pigments, which are manufactured at its Krefeld-Uerdingen site in Germany. The specialty chemicals company – which, with the tried-and-tested Bayferrox and Colortherm brands, is an internationally leading manufacturer of inorganic pigments – expects to gain a competitive edge thanks to its pioneering role and that its continuous investment in eco-friendly production processes will prove worthwhile. The EPDs not only enable the company’s customers to calculate the environmental impact of their products with much greater precision, but also constitute a sound basis for comparing the environmental impact of pigments from different raw material manufacturers.
The extent of the rise in awareness surrounding life-cycle assessments and EPDs is demonstrated by the extremely positive response of the construction industry to the launch of EPD pigment products from Lanxess. This applies above all to large building material manufacturers. Some of them want to initially use EPD-verified raw materials such as these iron oxide pigments primarily in highly sustainable product lines. Other manufacturers are increasingly looking to make life-cycle assessments and EPDs a basic requirement for the use of raw materials – and, as Lanxess has observed, this is happening sooner rather than later. This is why the specialty chemicals company has decided to offer such declarations for all the iron oxide pigments manufactured in Krefeld-Uerdingen from the second quarter of 2023.
Carbon neutrality targeted by 2040
Lanxess is continuing to drive investment in energy-efficient processes in the manufacture of pigments and considers this part of its business strategy. Among other things, the company has laid out a road map for further reducing the carbon footprint of its pigments, whereby greenhouse gas emissions at the main production site in Krefeld-Uerdingen are to be further reduced by around 50 percent thanks to new technology and, for example, the purchase of “green” electricity. These measures are part of the sustainability strategy of the specialty chemicals company as a whole and are aimed at reducing direct emissions associated with production (Scope 1) as well as emissions associated with the purchase of energy (Scope 2) and with the upstream and downstream value chain (Scope 3). Three years ago, Lanxess set itself the goal of achieving climate-neutrality for Scope 1 and 2 emissions by 2040. In 2022, the company expanded its climate-neutrality goal to encompass Scope 3 emissions, too. This is to be achieved by transitioning to sustainable raw materials, “green” logistics, and a climate-neutral product portfolio. The aim by 2030 is to cut Scope 3 emissions by 40 percent compared with 2015.
“Green” sodium hydroxide reduces the carbon footprint by 40 percent
One current example of Lanxess’s efforts in the area of sustainability is the recently agreed measure to also use “green” sodium hydroxide in the manufacture of granulated yellow pigments under the Bayferrox brand. The supplier of this vital raw material produces this base using renewable energies. It is deployed in precipitation processes that result in very high-quality yellow pigments with special properties such as high tinting strength and thermal stability. This “green” raw material helps to cut CO2 emissions during the manufacture of these product groups by as much as 40 percent per kilogram of pigment (Figure 5). Due to the exceptional sustainability of these yellow pigment product groups, Lanxess is planning to have them verified, too.
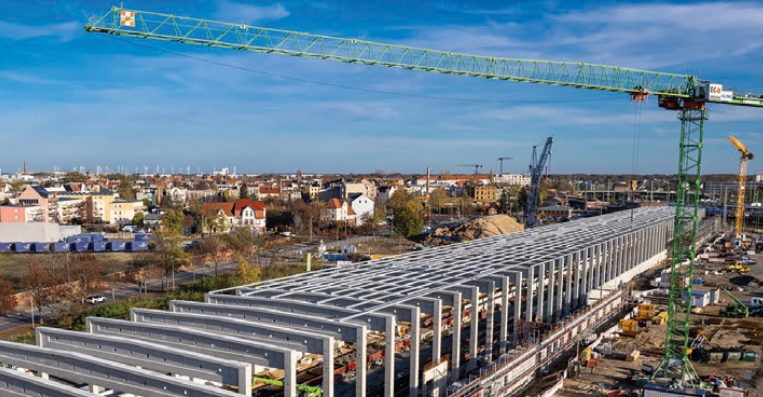