The mortar used to make the waterproof layer of buildings is called waterproof mortar. Waterproof mortar is an essential rigid waterproof material that can be used to improve the compactness of the mortar and achieve the purpose of impermeability and waterproofing through strict operating techniques or by incorporating appropriate amounts of admixtures with waterproof properties, synthetic polymers, and other materials. The cement mortar waterproof layer is generally also called a rigid waterproof layer.
Commonly used waterproof mortars can be divided into three categories: multi-layer cement mortar, waterproof mortar mixed with admixtures, and waterproof mortar prepared with expansion and non-shrinkage cement. Waterproof mortar mixed with admixtures can be divided into waterproof mortar mixed with inorganic waterproofing agents and polymer-modified cement waterproof mortar mixed with polymers.
In addition to various types of polymer waterproofing agents, domestically produced waterproofing agents used in waterproof mortars can be divided into three categories according to their main components:
① Waterproofing agent based on chloride metal salts;
② Waterproofing agent based on water-repellent substances (metallic soaps);
③ Waterproofing agent based on sodium silicate (i.e., water glass).
The first two types of waterproofing agents are mainly used for waterproofing mortars formulated with the above three types of waterproofing agents. Sodium silicate waterproof mortar is generally used in engineering to repair leaks and treat surfaces due to its quick-setting effect and adhesion.
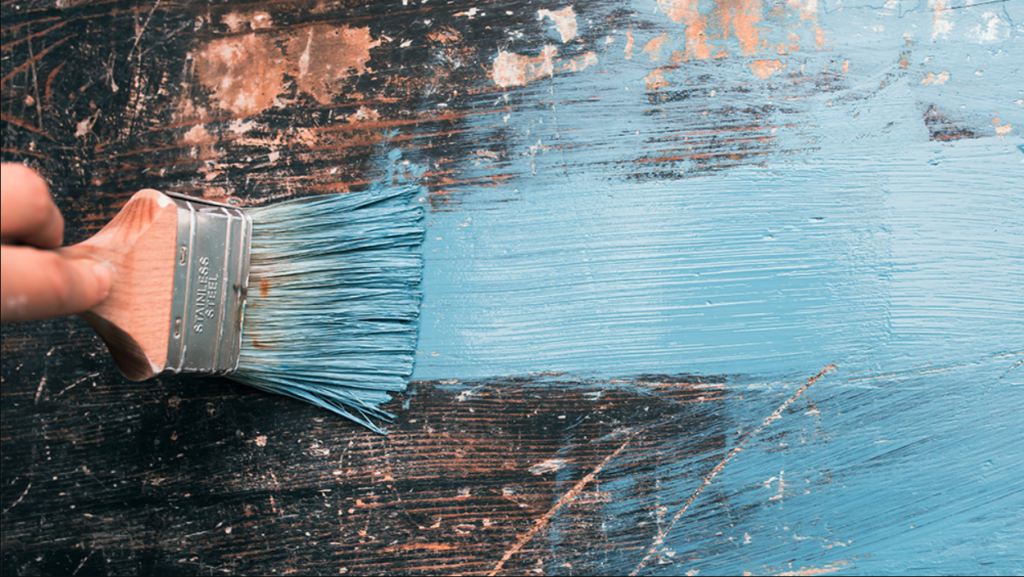
Compared with other waterproof materials such as membranes, metals, and concrete, cement mortar waterproofing has specific functions, simple construction operations, low cost, and easy repair. However, due to its poor toughness, brittleness, and ultimate tensile strength, It is low and easy to crack as the base layer cracks, so it is challenging to meet the increasingly higher requirements of waterproofing projects. To overcome these shortcomings, in recent years, it has been essential to use high molecular polymer materials to make polymer-modified mortar to improve the tensile strength and toughness of the material.
According to different construction methods of waterproof mortar, it can be divided into two types: one is waterproof mortar constructed using high-pressure spray gun machinery. This waterproof mortar has high density and can enhance the waterproof effect. However, this small construction machinery needs to be improved. , the operating technology is more complex, and the quality is difficult to control, so it is not widely used in China and is only used for the reinforcement of concrete projects or other water storage projects with special requirements; the other is the large-scale application of manually applied waterproof mortar for waterproofing, this kind of mortar waterproofing mainly relies on specific construction process requirements or adding a particular waterproofing agent into the mortar to improve the compactness of the cement mortar or improve the crack resistance of the mortar, thereby achieving the purpose of waterproofing and preventing seepage.
2. Polymer cement waterproof mortar
Polymer cement waterproof mortar, also called polymer-modified cement waterproof mortar, is a type of rigid waterproof material evenly prepared by stirring and mixing cement, aggregate, rubber latex, or resin-emulsion, as well as stabilizers, defoaming agents, and other additives.
Polymer waterproof mortar is a certain amount of polymers, such as silicone, chloroprene latex, and acrylic emulsion, mixed into cement mortar to make the mortar have good impermeability, crack resistance, and waterproof properties. For example, after an organic silicone waterproofing agent is mixed into cement mortar, under the action of water and carbon dioxide in the air, methylsiloxane can be generated, which is further condensed into a network methyl silicone waterproofing membrane, which can penetrate the base layer and block the cement mortar. The internal capillary pores increase the compactness and impermeability, thus playing a waterproof role; another example is that after the latex resin polymer is incorporated into the mortar, it can be evenly distributed on the surface of the fine-grained aggregate inside the mortar. Condensation under certain temperature conditions causes cement, aggregate, and polymer to form a complete network film with each other, sealing the passage of the mortar gaps, thereby preventing the immersion of the medium, significantly reducing the water absorption of the mortar, and making it impermeable. Capacity has been improved accordingly.
Many polymers can be blended with cement, including natural and synthetic rubber latex, thermoplastic and thermosetting resin emulsions, water-soluble polymers, etc. The various properties of its polymer cement mortar depend to a large extent on the characteristics of the polymer itself and its blending amount in the mortar. If the blending amount is low, the performance of the mortar will not meet the requirements. If the blending amount is high, the cost is high, and the adhesion and dry shrinkage also deteriorate. Therefore, from practicality, low price, and waterproof effect, polymers and their polymer cement mortars should meet quality requirements.
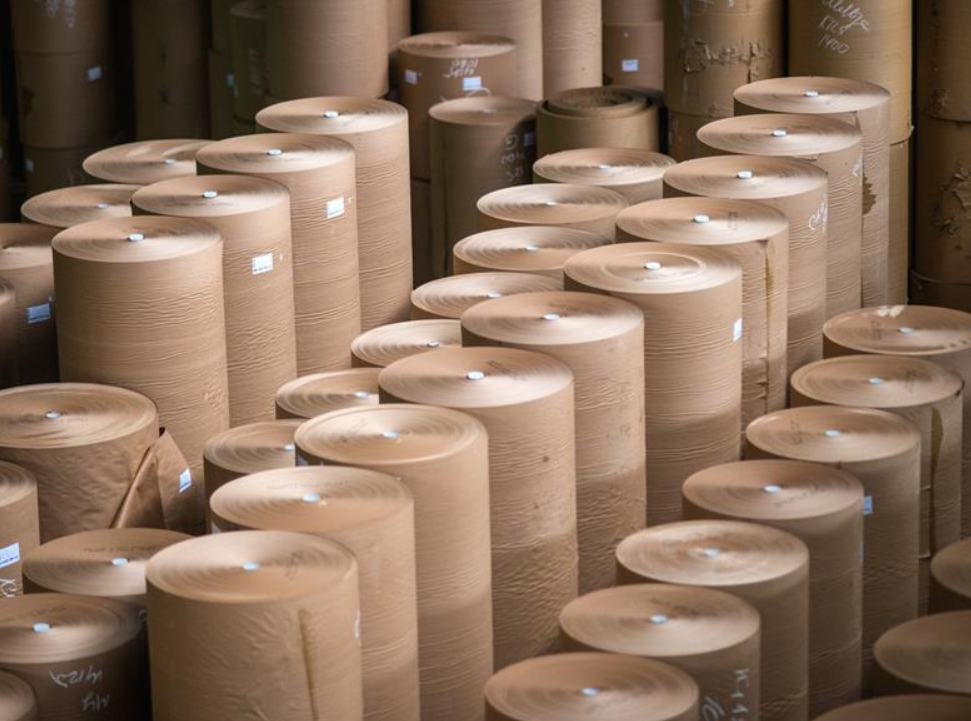
To make the polymer emulsion chemically stable against a large number of polyvalent metal ions in the cement hydration product and mechanically stable against the shear force generated during mixing, and to avoid precipitation and agglomeration of latex during the mixing process, the mixing process is During the emulsion mortar process, a certain amount of stabilizer must be added. In addition, due to the surface activation effect of the stabilizer in the latex, many bubbles will be generated during stirring, resulting in an increase in the material’s porosity and a decrease in strength, thus affecting the quality of the mortar. Therefore, when adding stabilizers, an appropriate amount of defoaming agent must also be added, and on the premise of meeting the above chemical and mechanical stability requirements, the minimum penetration amount must be used to reduce costs. There are many types of stabilizers and defoaming agents. Depending on the type and variety of the selected emulsion, the selection can be matched, and reasonable technical and economic results can be obtained.