Wood fiber is a white or off-white powdery fiber made from high-grade natural wood rich in lignin (such as fir and beech), dietary fiber, vegetable fiber, chemically treated, extracted, and ground. Wood fiber is a natural fiber that absorbs water and is insoluble in water. It has excellent flexibility and dispersion. Adding appropriate amounts of wood fibers of different lengths to cement mortar products can enhance shrinkage and crack resistance, improve the thixotropy and sag resistance of the product, prolong the opening time, and play a specific thickening effect.
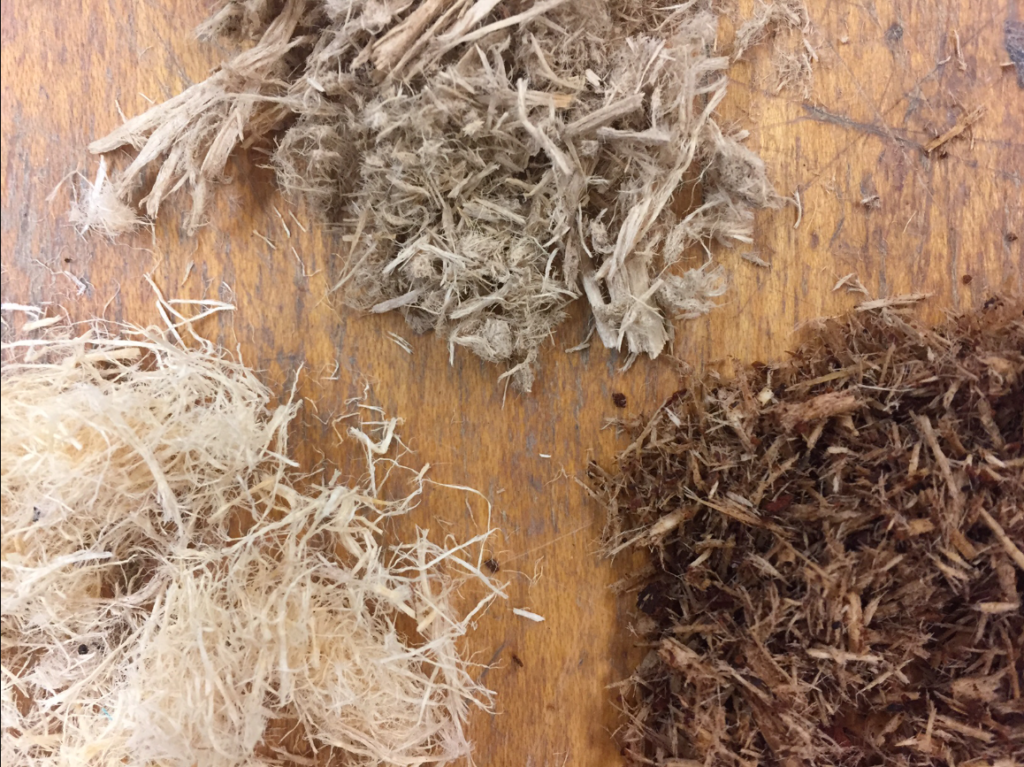
Wood fibers are porous long fibers with an average length of 10 μm to 2000 μm and an average diameter of less than 50 μm, which mainly depends on the type of wood fiber. For example, the diameter of pine is 18 μm, and the diameter of beech is 35 μm. The specific gravity of wood fiber is 1.3g/cm³~1.5g/cm³; the moisture content is 6%~8%. It absorbs water efficiently in the air and should be stored in a dry place; it is insoluble in water and organic solvents and resistant to dilute acids and alkalis. Temperature resistance is 180℃, 1h~2h. It is shrinkable, non-toxic, and can replace 30%~50% of asbestos; the water penetrating the wood fibers’ pores has a freezing point of -70℃, so it is resistant to freezing and thawing. The pH value is 7.5. Wood fiber also has specific high-temperature resistance, acid and alkali resistance, and frost resistance, so it has a wide range of uses.
Natural wood fiber and methylcellulose ether are two completely different products in practical applications. Wood fiber is made from high-grade natural wood such as beech and fir, which is pickled and neutralized, then crushed, bleached, rolled, and sieved. The obtained water-insoluble natural fibers of different lengths and fineness are essentially different from methylcellulose ether dissolved in warm water. Although some functions of wood fiber are similar to those of methylcellulose ether, such as thickening and water retention, its thickening and water retention effects are far lower than those of methylcellulose ether. Wood fiber cannot be used alone as a thickener, and water-retaining agents are used.
The most prominent feature of wood fiber is its material’s own flexibility and unique three-dimensional network structure. These characteristics determine that wood fiber plays a role in reinforcing and resisting cracking and anti-sag in the dry mortar system rather than thickening and retaining water. Although the raw material for producing methylcellulose ether is also wood or short cotton fiber, its production process differs significantly from wood fibers. Therefore, the prices of the two are very different. In practical applications, methylcellulose. The main functions of ether are water retention and thickening, so we must be clear about the various uses of the two when using them. Different types of wood fiber products with different lengths and fineness are suitable for different application fields. The size of medium and short wood fibers is generally 40μm~1000μm, which can be used in dry mortar products, and the length is 1100μm~ Long wood fibers of 2000 μm are usually only used in emulsion-type adhesives and paste putties. This is because long fibers are limited in the dry mixing of dry mortar products and are not easy to disperse and easy to agglomerate.
2. Pigment
Pigments can be divided into liquid pigments and powder pigments according to their material state; they can be separated into organic pigments and inorganic pigments according to their chemical properties; they can be divided into natural pigments and synthetic pigments according to their sources.
The pigments used in dry powder mortar are generally inorganic powder pigments. Inorganic powder pigments include iron oxide, chromium, and lead series. Among them, the pigments used in dry mortar are typically in the iron oxide series. Alkali-resistant mineral pigments will not have any harmful effects on cement. Commonly used ones include iron oxide (red, yellow, brown, black) and ultramarine (blue).
Things to note when applying pigments to dry-mixed mortar are as follows:
(1) Pigments cannot affect the hydration and strength growth of cement, gypsum, and other cementitious materials. Chromium and lead series are powdered, inorganic pigments, but lead ions are a retarder for cement and are heavy metals that are harmful to the human body and cannot be used in dry mortar. Suitable pigments for dry mortar are iron oxide series;
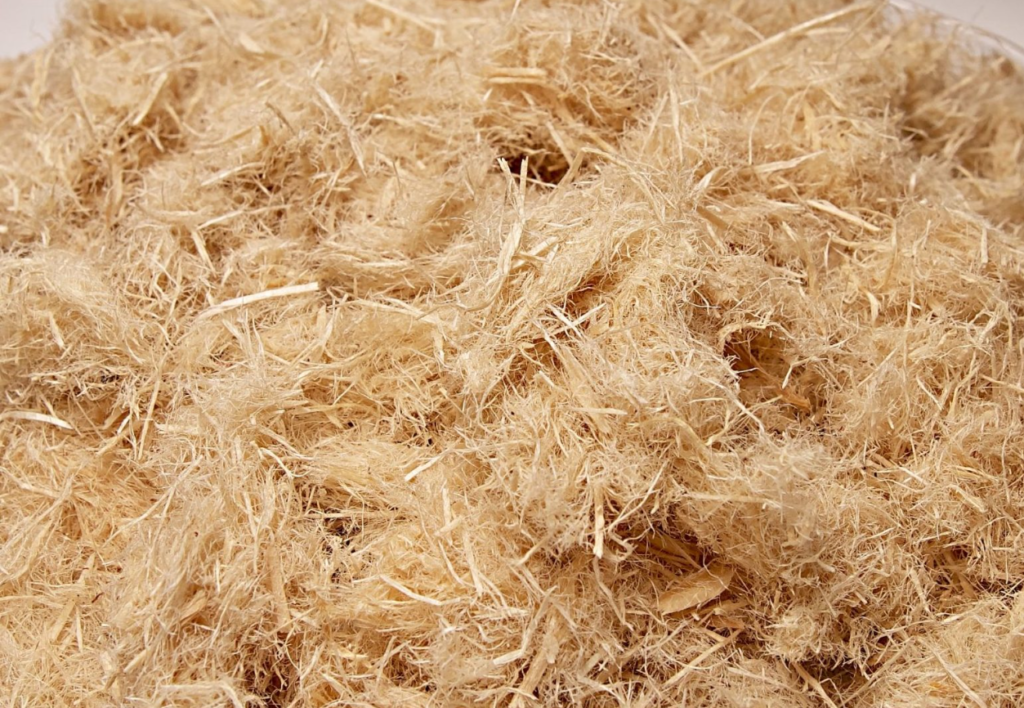
(2) The pigment must be compatible with the constituent materials of dry mortar, such as cement. Most organic pigments are incompatible with inorganic materials such as cement and cannot be used for coloring dry mortar. Carbon black is an inorganic powder pigment but incompatible with inorganic materials such as cement. Cement is incompatible and affects the hydration of cement. It is not suitable for use in dry mortar;
(3) When making red, brown, or black cement mortar, alkali-resistant mineral pigments can be added to ordinary Portland cement instead of white Portland cement.
Storage of ready-mixed mortar
After the ready-mixed mortar is transported to the construction site by a particular transport vehicle, in addition to direct use, corresponding storage measures should be taken according to different environmental conditions to ensure the quality of the ready-mixed mortar.
Ready-mixed mortar must be stored in a sealed container that does not absorb water. The maximum temperature where the mortar is stored should not exceed 37°C, and the minimum temperature should not be lower than 0°C. Shading measures should be taken in summer, and insulation measures should be brought in winter. Waterproof measures should be taken when loading and unloading the mortar, and it is strictly forbidden to add water to the mortar during storage. Mortar must be used within the specified time.
The container for storing mortar should be convenient for storage, transportation, cleaning, and loading and unloading. Containers for storing mortar should be clearly labeled to ensure first in, first out, first save, first use, last save, and later use. It is strictly prohibited to use mortar that has exceeded the setting time, and it is not permitted to store and mix different types of mortar. When the mortar is used up, the container in which it is stored should be cleaned immediately for reuse.